Understanding Imitation Wood
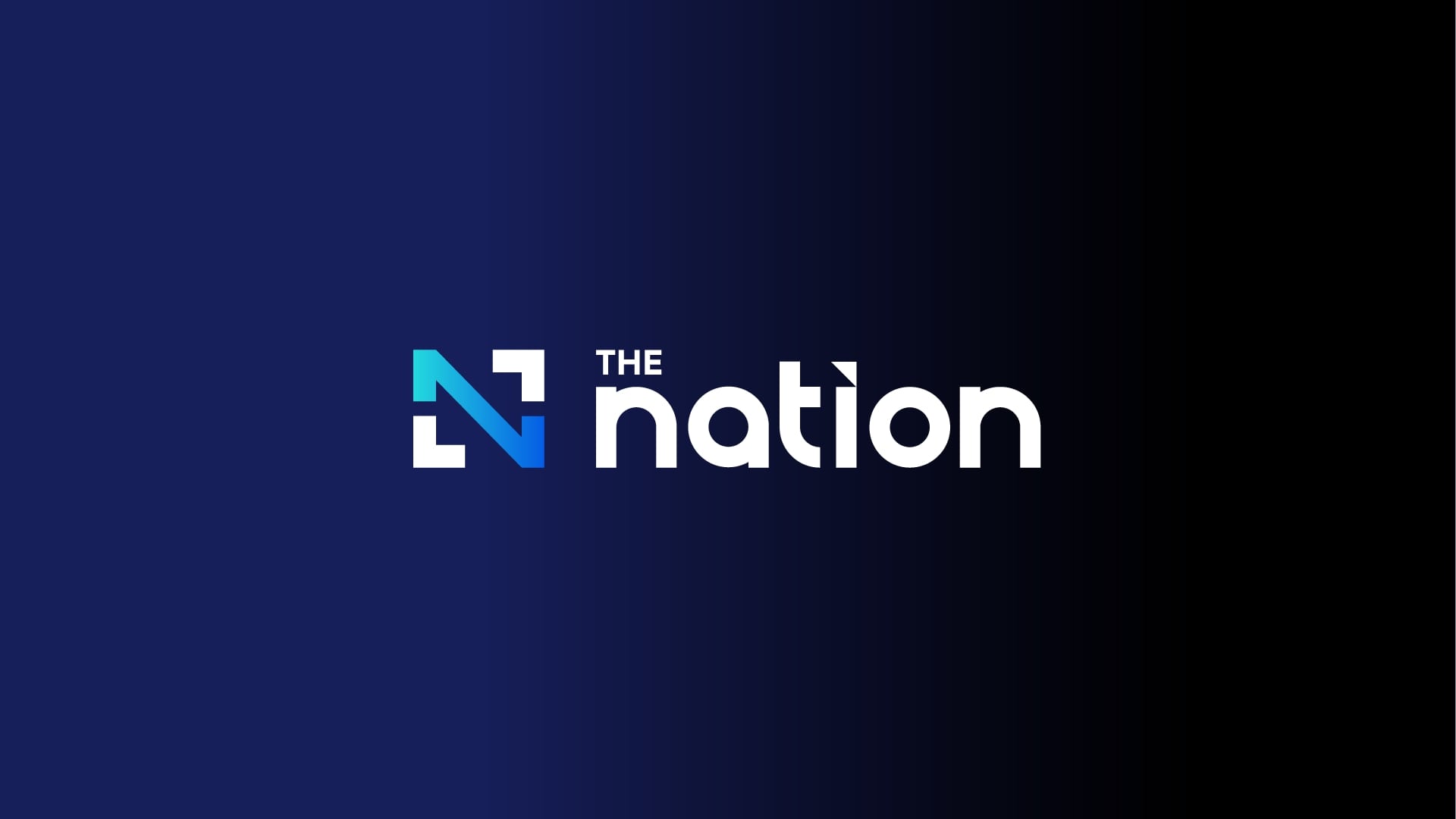
Wood has always been an extremely popular material for construction, but its popularity has decreased as the market price of timber has risen.
Some of wood’s properties limit its utility. Wood bends and buckles with variations in temperature and attracts termites and other pests. For these reasons, imitation woods have stepped in to become an acceptable substitute for timber.
Imitation woods are manufactured from a variety of materials including polymers, PVC and plastics, but the type most commonly used is a composite containing cement. It costs less than wood and is not vulnerable to termites and vermin infestation. It resists heat, cold, and moisture, which decreases its susceptibility to material contraction and expansion and consequently commends it for both indoor and outdoor use. Consumption of imitation woods also has the advantage of not participating in the depletion of natural resources.
Cement is the primary stable component in cement-composite imitation wood. These imitation woods can be categorised into two types depending on strength and other mechanical properties. Fibre cement results from the mixture of cement and wood pulp from pine trees, banana palms, bamboo or recycled paper. Wood cement board is a blend of cement and compressed pine or eucalyptus wood particles.
These two types are manufactured differently. With fibre cement, raw materials are blended into a dense fluid concentrate, which is released on to a conveyor belt in layered sheets until the desired thickness is achieved. The sheets are then taken away to dry and cure before trimming and finishing. This process resembles the manufacture of paper, giving the material the nickname “paper tile”.
Production of wood cement board proceeds differently. The first step consists of dusting component powders onto metal plates to the desired thickness, then pressing the stacked metal plates using a high-pressure compressor. Afterwards, the composite is left to cure for a period of time before it is finished and trimmed to size. This production process allows for a homogenous and contiguous surface that resists water. By contrast, fibre cement, which relies on the overlapping of composite layers to develop shape and appearance, exposes the material to moisture.
Differing steps in the production process distinguish fibre cement further into types. The Hatschek process involves the formation of sheets of material by rotating fibre and cement concentrate through a cylindrical sieve in order to de-water the solution. As the sieve is pulled under the concentrate in a vat, water runs through the sieve and deposits a soft porous film of fibres and cement on the surface of the sieve. Films are layered to the desired thickness to form one sheet and laid to dry and cure. The flow-on process requires the drying of sheets at room temperature, making the products of this process more fragile than those of the Hatschek process and necessitating thicker and rigid, less malleable fibre cement sheets in order to enhance durability.
Fibre cement and wood cement board products can be found in 1.20 x 2.40 metre dimensions and can be immediately employed in construction. We are familiar with these materials by the terms “ceramic tile,” “fibre cement siding,” “fibre cement cladding,” and “fibre cement panels.” Sheets of smaller measurement can be used as decorative alternatives for wood and can be identified by the trade names “wood paneling,” “wood siding,” “wood fencing,” or “faux bois.”
All of these imitation wood options continue to gain in popularity in home construction and interiors.
KittiwootChaloeytoy Department of Architecture, Faculty of Architecture, Chulalongkorn University.