Myanmar courting global producers
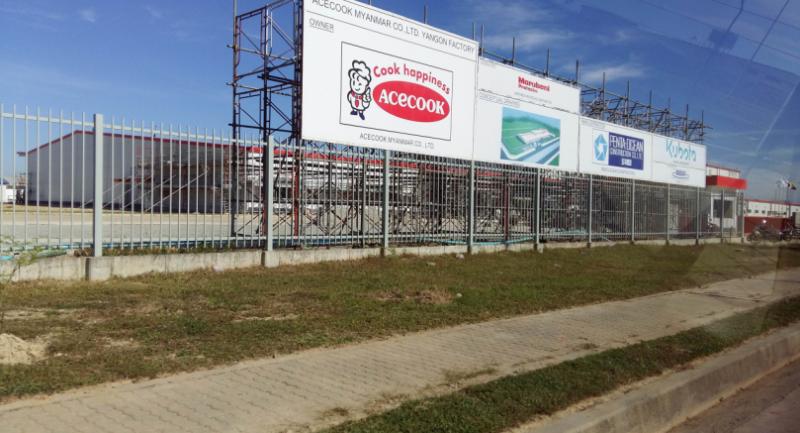
THE MYANMAR authorities have sped up efforts in recent months to increase the country’s attractiveness for global manufacturers.
The latest move was revealed in September by the Myanmar Investment Commission (MIC) and concerns the move to allow local and foreign investors into industrial zones across the country. This follows requests by companies from Hong Kong and South Korea which proposed to establish industrial zones for garment factories.
According to Aung Naing Oo, commission secretary, the MIC was discussing potential locations with regional governments. Yangon and Bago are the locations with the most potential, thanks to their proximity to ports and jetties. Once permitted, the investors will be required to submit progress reports to the MIC every three months. The investment supervisory department will conduct regular checks on industrial zone operations.
“Industrial zones for garment factories are planned as we have already received some proposals. Foreign companies are making preparations,” he said.
The move is considered a win-win for Myanmar and foreign investors.
According to the 2014 national census, 65.6 per cent of Myanmar’s 52 million people are of working age (15-64 years old). Only 4 per cent were unemployed. However, as about 70 per cent of households depend on agriculture, Myanmar’s per-capita income is among the lowest in the world, at only US$ 1,203 (Bt43,000) in 2015 compared with $824.19 in 2011. Industrialisation is expected to boost the individual and national income, while creating jobs for millions of Myanmar nationals who are either working in the agricultural sector or working overseas.
However, investment in the |manufacturing sector has re-|mained low, despite renewed |export privileges from Japan and |the European Union. According |to Toe Aung, the director of the Urban Planning Department under the Yangon City Development Committee, only 23 per cent of |the working-age workforce works |in the manufacturing sector. According to the Directorate of Investment and Company Administration (DICA), the combined investment into the sector since 1988 until August 2016 was only $6.92 billion, approximately 10 per cent of the $64.4 billion in foreign direct investment inflows to the country during that time. FDI inflows to the sector jumped in the 2013-14 fiscal year, but eased in subsequent years: from $1.83 billion in the 2013-14 fiscal year, to $1.5 billion in the 2014-15 fiscal year and $1.06 billion in the previous fiscal year. In the current fiscal year, from April to August, the approved investment sum, for 13 projects, was worth only $336 million.
The United States’ move to end all sanctions injected a new expectation regarding the economy, which hopes that its low labour cost – at 3,600 kyats a day (Bt100) – would attract new investment, particularly in the garment industry. Myanmar has 400 clothing factories and more than 350,000 workers in the industry, according to the Myanmar Garment Entrepreneurs Association. As| of February, there were 171 foreign-owned factories, 196 privately owned establishments and 22 joint|ventures.
Land scarcity
There is pressure for the government to levy property taxes and seize inactive industrial land plots, in order to release more land for manufacturing activities. According to the Internal Revenue Department, there are 37,076 industrial land plots across the country, 7,194 of which are idle, including more than 2,000 plots in the Yangon region and more than 1,000 plots each in Shan State and Mandalay Region. There are 2,339 vacant plots and 1,299 idle warehouses in industrial zones stretching across 1,787 hectares in Yangon.
Speaking to the Parliament in August, Nilar Kyaw, Yangon Region’s minister for electricity, industry and transportation, said the regional government would survey industrial zones in the region and would reclaim inactive land plots.
According to lists compiled by the YCDC, the government reclaimed 10,432 plots of land in 2012 and 64 hectares of land for industrial zones in the region. According to the Strategic Urban Development Plan of Greater Yangon 2040, about 40 per cent of this land remains vacant and skyrocketing land prices continue to hamper Yangon’s industrial development.
“The establishment of industrial zones can create more employment opportunities. We can employ about 500-600 workers if we establish a garment factory,” said YCDC's Toe Aung.
Foreign investors have complained about scarcity of industrial land and insufficient supporting infrastructure. This results in extraordinarily high land prices.
Aye Thiha, chief executive officer of Thiha Group, said that at $150,000 per rai or approximately Bt5 million, land prices in Yangon are way above those in Vietnam.
But he is hopeful that land prices should decline next year thanks to the government’s initiatives to increase land availability.
Obstacles
“Land prices should decline next year as the authorities are reclaiming undeveloped land in 29 industrial estates in Yangon and releasing the land to the public,” he said at a Bangkok Bank seminar in Bangkok in September.
Thiha Group is the local partner of Thailand-based Millcon Steel which set up a facility in the Thilawa Special Economic Zone.
“Land prices in the zone are a bit more expensive but the zone offers greater ease for the operations. For newcomers, I suggest you operate in SEZs which offer much greater services,” Aye Thiha said.
It took the joint venture Mill Thiha Gel two months to obtain the investment permit. Construction took another 14 months and that was followed by the import of machinery. The facility commenced operations in November, about 18 months from the day the joint venture formation was announced.
Access to land is one of the most frequently cited severe obstacles by businesses in Myanmar, according to a UN Escap survey released in May 2015. In the survey, other severe obstacles cover corruption and access to skilled labour and technology. Access to finance is also found to be a major obstacle, especially by local small and medium-sized enterprises.
Access to infrastructure like electricity and water are not rated as severe obstacles overall, but they are more severe in some areas of the country. It is a key reason why most foreign investment projects tend to locate in Yangon Region, considered the most developed in terms of infrastructure, which also includes ports.
Investing in Myanmar can also entail other challenges.
Pakainay Leng-Ee noted that aside from land prices, all companies in Myanmar should bear in mind that they may have to get their hands on logistics. Plus, workers are keen to take simple orders and they will not devise alternative solutions on their own.
“It was a Wild Wild West. It’s getting better today,” said Aye who spent 15 years in the United States before returning home to start his own business that includes a pizza restaurant.
Nattawin Phongphetrarat, vice president of the Thai Business Association in Myanmar, noted that direct experience points to corruption being less worrisome. The more important note is that any companies looking for investment opportunities in Myanmar should be ready in terms of personnel, finance and product quality.
“You need to understand that |the country has been shut off from the world for a long period of time. The way of thinking is not like |anywhere else in the world. There |is not a supply chain in the country and any investors have to devise |their own plan. This could complicate investment projects,” Nattawin said.
Foreign companies should also be aware that their operating costs will be higher than local costs – mainly driven by rent and cheap labour (many family members are serving the companies for free). But foreign investors’ advantages lie in the quality of services and products, he noted.